Winter Projects
It was a busy winter. We had a long list of things we wanted to get done on the boat while she was out of the water.
Task one was to deal with the barnacle growth, which was extensive. I was pretty disappointed with the effectiveness of the Trilux 33 antifouling paint. I was also disappointed to discover that Allures had not antifouled the bow-thruster leg and propellers. The assembly became a barnacle farm. At least now we know why the bow-thruster stopped working.
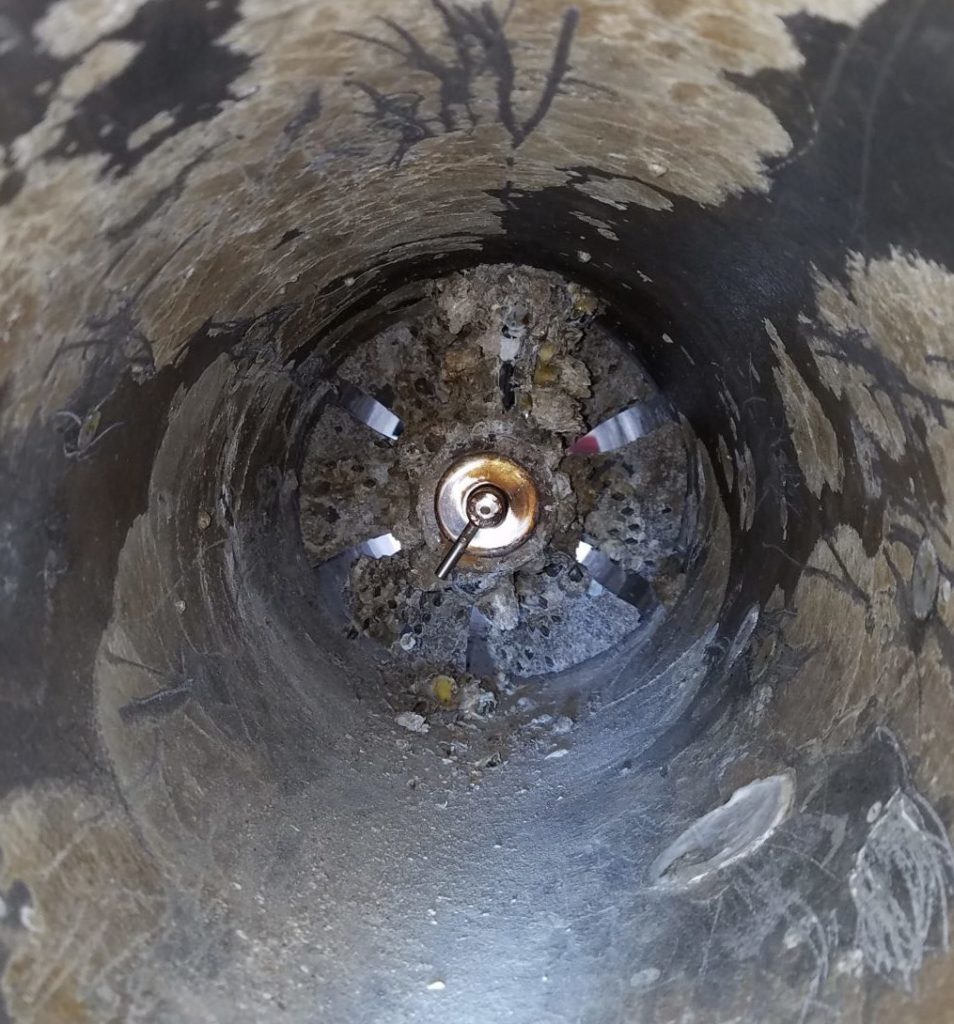
Many hours over multiple weekends were spent scraping barnacles. I decided to remove the bow-thruster leg and propellers to properly clean and prepare them. As is often the case with boat projects, this became more complicated when the drive leg broke on removal. Fortunately, we had plenty of time to order a replacement and properly antifoul it before installation.
For the 2019 season we have switched to Pacifica Plus antifouling. It is better for the environment than the Trilux 33, less expensive, and according to Interlux (the manufacturer) more effective. Interlux advised that we would get better results with the Pacifica Plus if we applied many coats. Perhaps they were just trying to sell more paint, but with memories of hours of barnacle scraping I decided on 4 coats of the new paint.
A rope cutter for our propeller was on our wish list as a potential safety upgrade. After much research I believe the only rope cutter manufacturer for out propeller / sail drive configuration is Delot & Company. Other than the stress of drilling holes in our expensive propeller and Delot shipping the wrong anodes, the installation was straight forward.
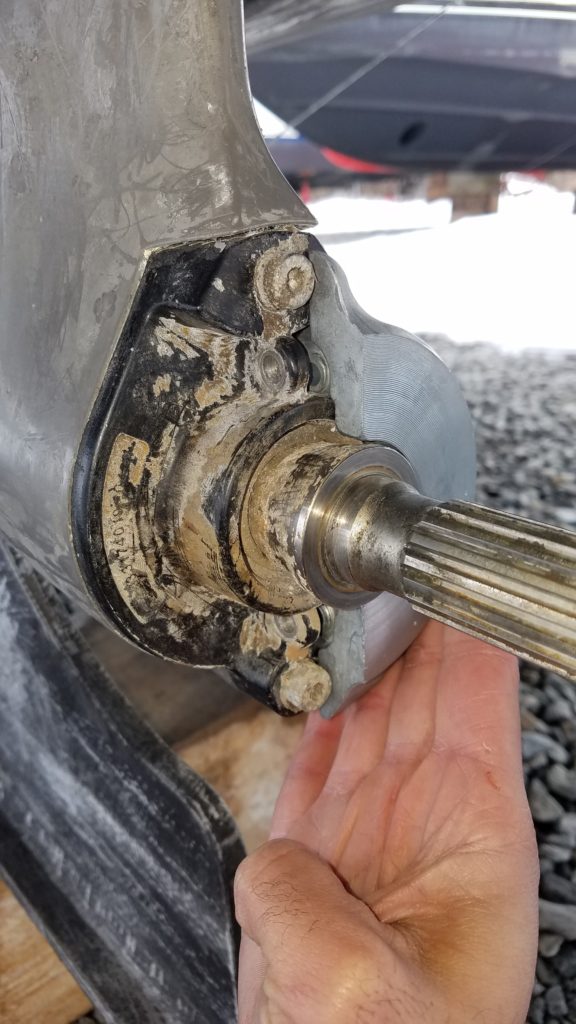
Our largest project this winter (other than scraping barnacles) was the installation of our watermaker. This project I really enjoyed. It was very mechanical. I enjoyed figuring out how to fit all the parts to ensure elegant connections. Overall the project was a great success. ECHOTec, the watermaker supplier, has been one of the most professional marine companies we have dealt with. Every part emanated quality.
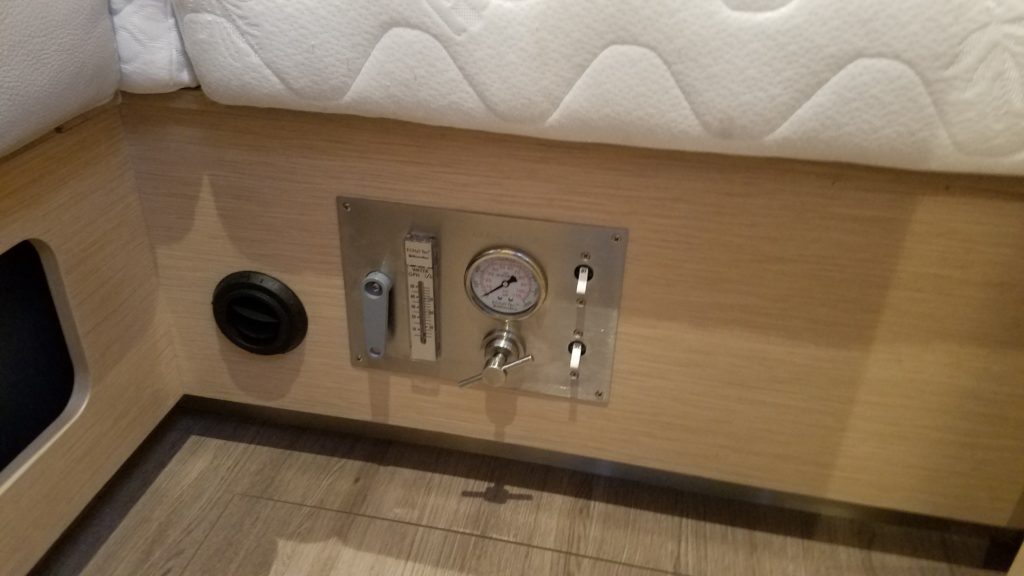
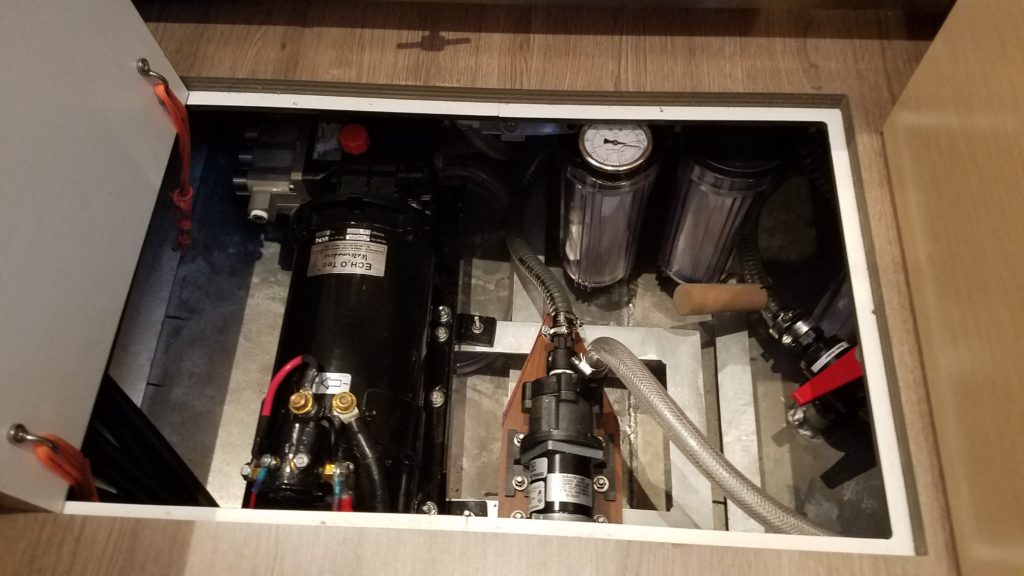
We opted for a relatively high capacity, 32 gallons (120 ltr) / hour 12V watermaker. This will push the limits of our batteries. However, we expect our next batteries will be lithium polymer. Then, the watermaker and batteries will be better balanced. For now, we will need to be cautious about battery charge state while making water.
Another fun winter project was creating a semi-custom laminated map to protect the salon table. As an architect, this was a perfect project for my skill set. As expected, we think it came out perfect!
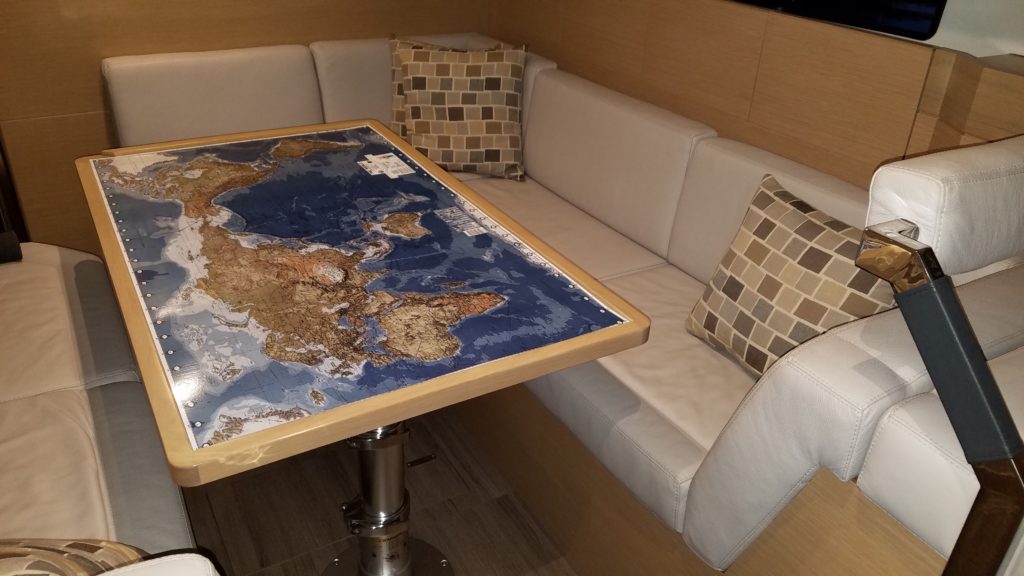
There is a saying that goes something like, “a sailor is only as happy as the number of lines he can control”. Not sure if that is true, but I was frustrated that I could not change the twist of the head-sails without unloading them, going to the leeward deck, and adjusting the cars. This winter I upgraded our cars to ride on ball bearings and installed blocks so they can be adjusted by a line from the cockpit, and I am happy, so perhaps the saying is true.
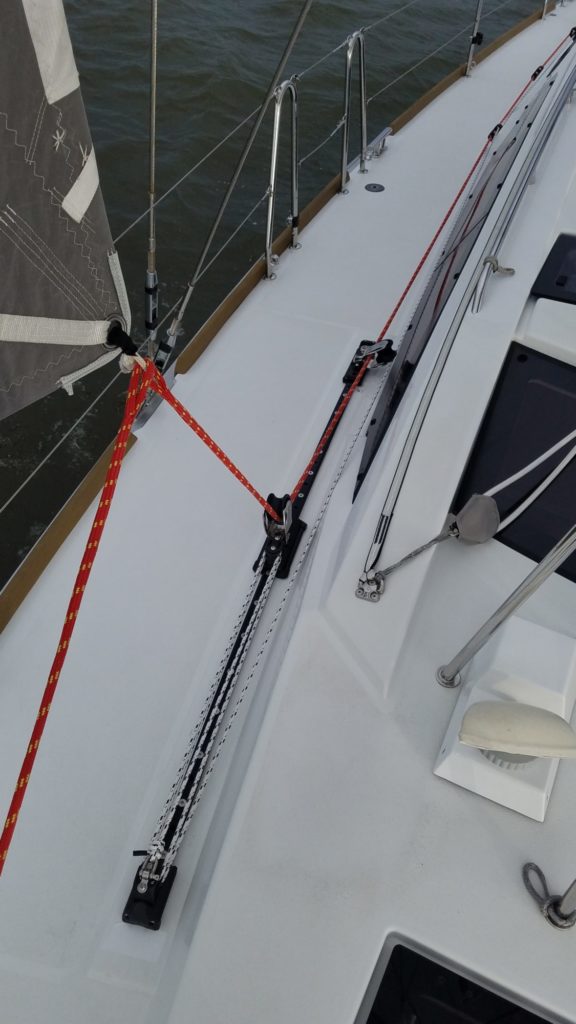
In anticipation of some ambitious ocean crossings, we purchased a Jordan’s Series Drogue from OceanBrake, another very profession company. We decided to go with a full Dyneema version of the drogue to keep bulk and weight down so it is easier to handle and store. For those unfamiliar, a series drogue is arguably the best way of keeping Gerty under control in terrible conditions. The drogue is deployed off the back of the boat and acts like a giant kite tail. As the boat is blown downwind and surfs waves, the drogue keeps the stern oriented towards the wind and waves. It also slows the boat to a crawl. Most importantly, it does this without active crew participation. We can hide inside waiting for the worst to pass.
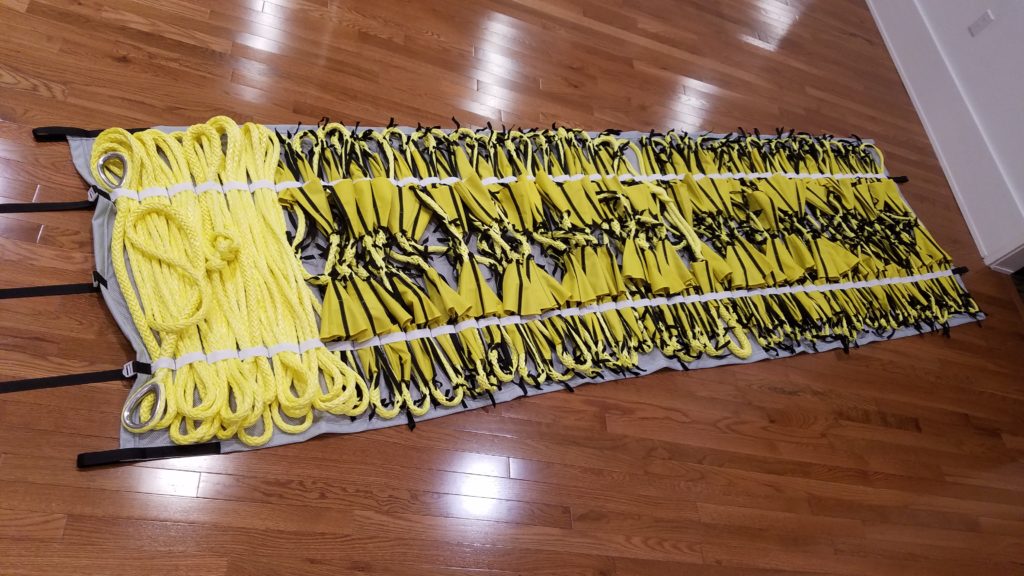
The drogue restrains the boat from sliding down large waves. The forces involved can be huge. Therefore, we have also installed two heavy duty pad-eyes at the stern quarters to attach the drogue and avoid chafe. Fortunately the aluminum hull plate thickness at this location is 5/8” (16mm), one of the strongest parts of the hull.
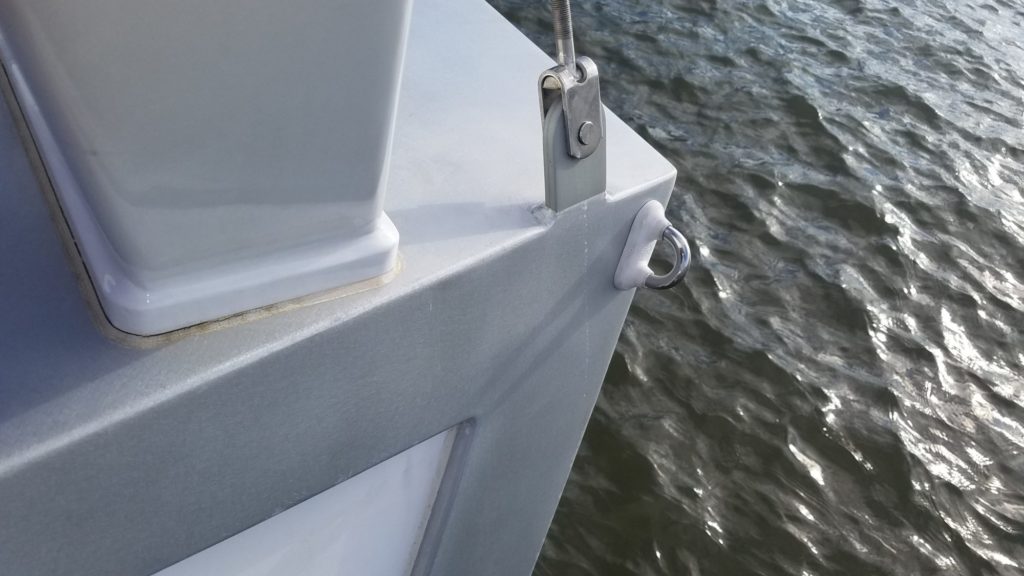
Last season the mainsail batten pockets chafed on the upper shrouds. This winter I sewed Dacron covered HDPE plastic chafe guards to the problem spots. I believe this will effectively protect the sail. If not, I will consider adding some shroud covers.
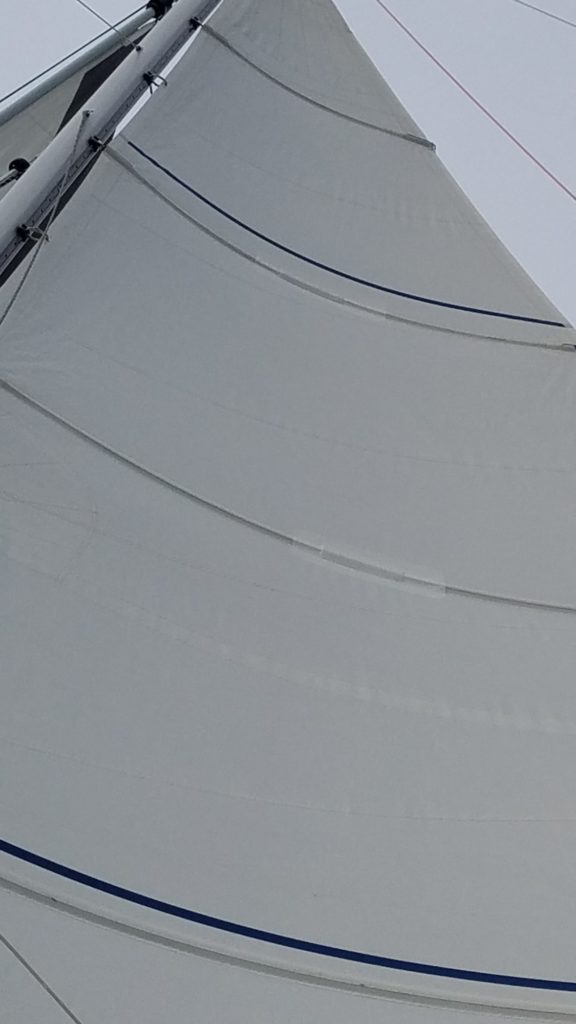
Jill’s complaint last year was that on hot days there was not enough air movement in the head. As usual, she was right. So a priority this winter was to install a fan in the head. These kind of projects take a while since sections of the headliner (ceiling) must be removed.
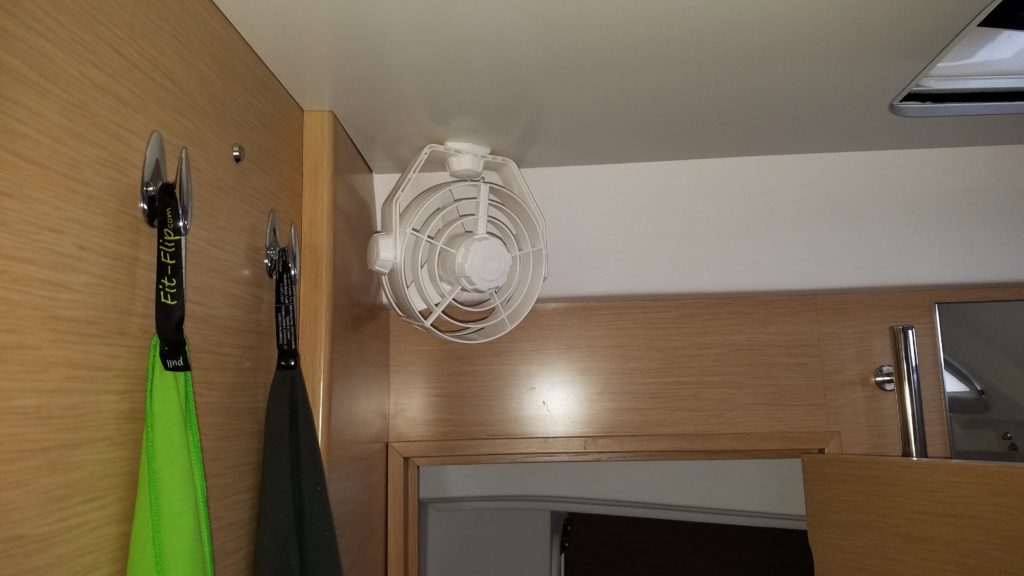
My final sizable project of the winter was to better secure our propane tanks. My solution was to secure two halves of a 12″ (305mm) PVC pipe coupling. Each half becomes a cradle for a tank. I still get a rush when a design idea works out so well.
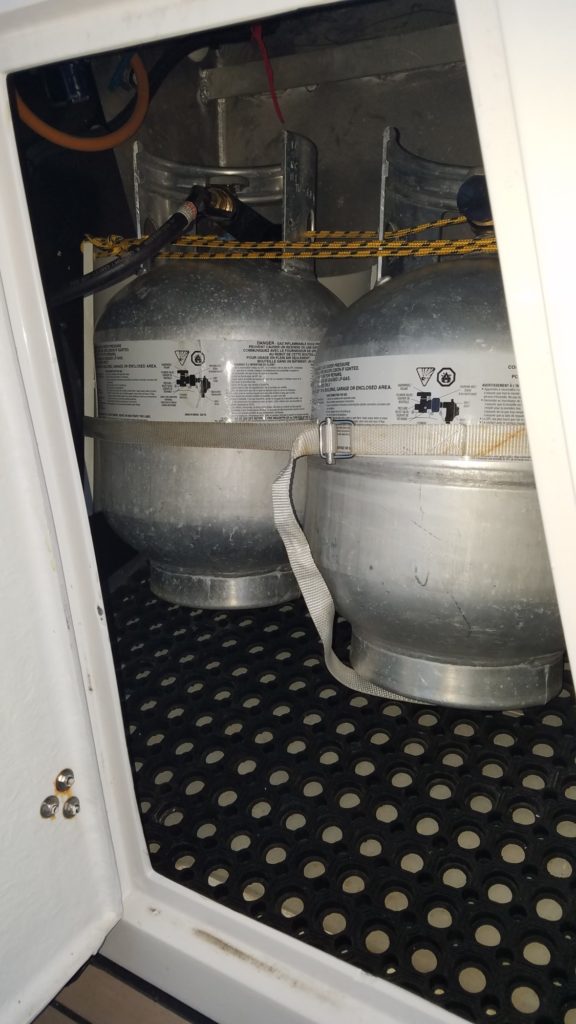
Add to all the above some bilge storage improvements and ordering many spare parts, and it made for a busy winter of boat work.
With that all behind us, Gerty was lifted off her jack stands on April 11th and transported back to where she belongs, the water.
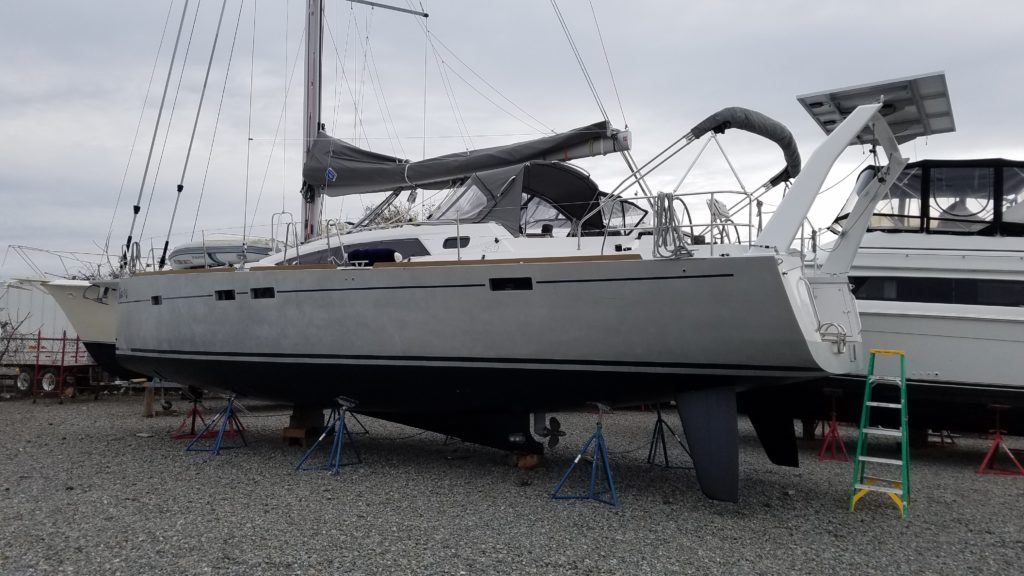
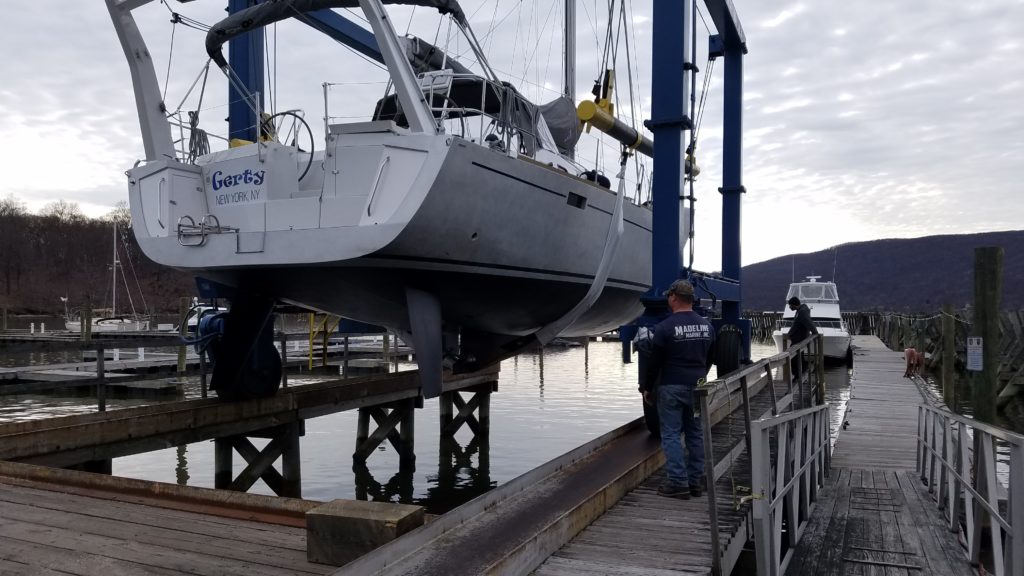
We installed all the halyards and sails. Jill took her first trip up the mast because – well because it is fun. But also, she had to re-feed our pole lift line which we accidentally removed without a tracer.
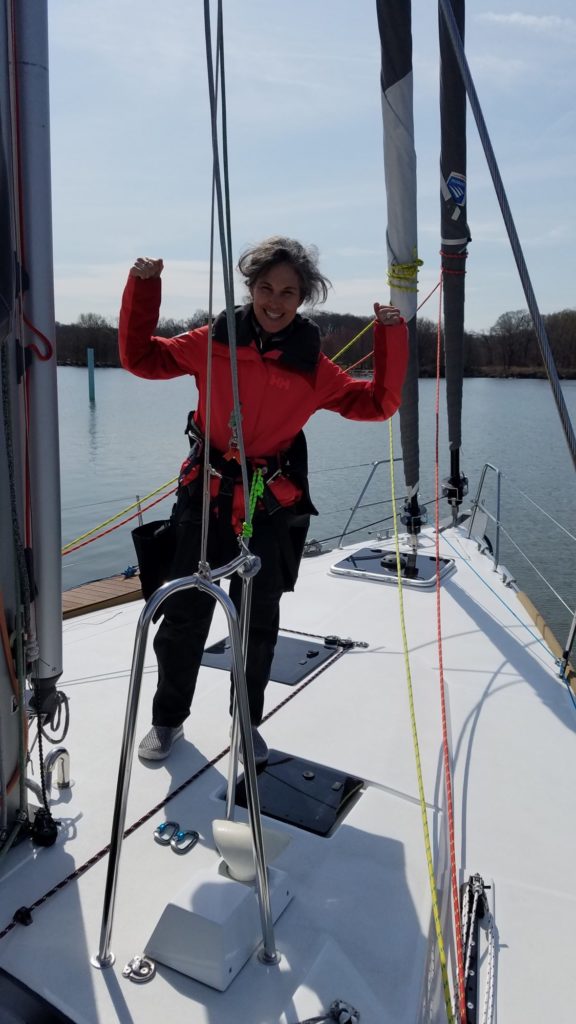
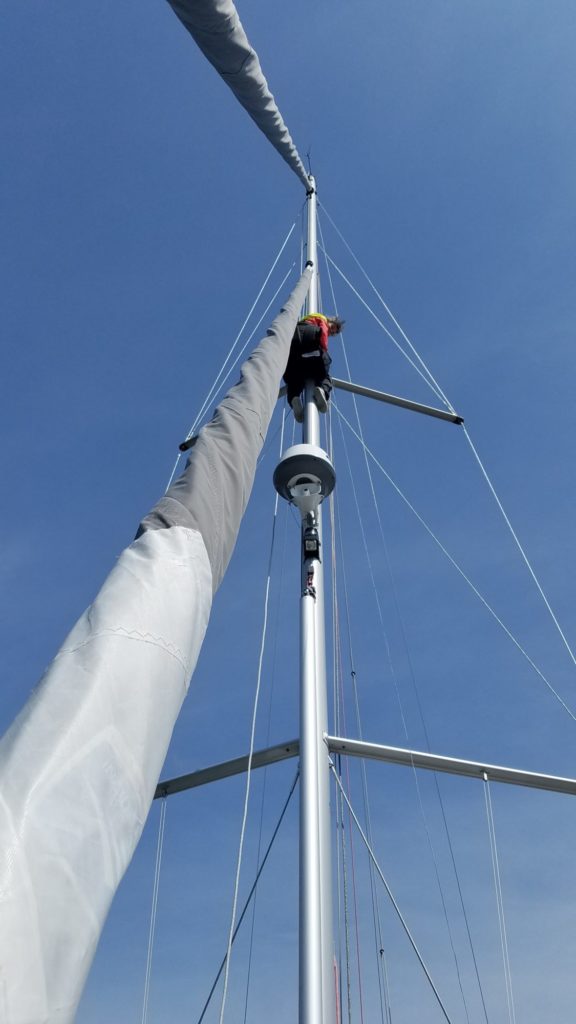
I also went up the mast and did a full inspection of the ring. All looked great except for the large bone “someone” left on top of the mast. I wonder if one of the bald eagles I saw throughout the winter ate lunch up there.
On Sunday we took our first sail of the season. Everything in our lives now seems balanced and better. It was a good and productive winter with some great trips, but we are happy to be sailing again!
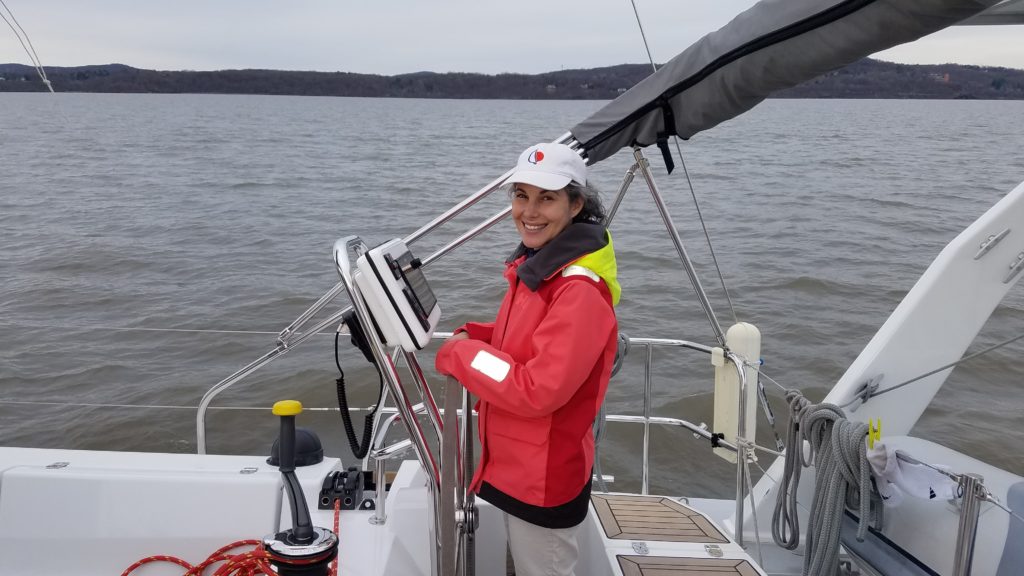
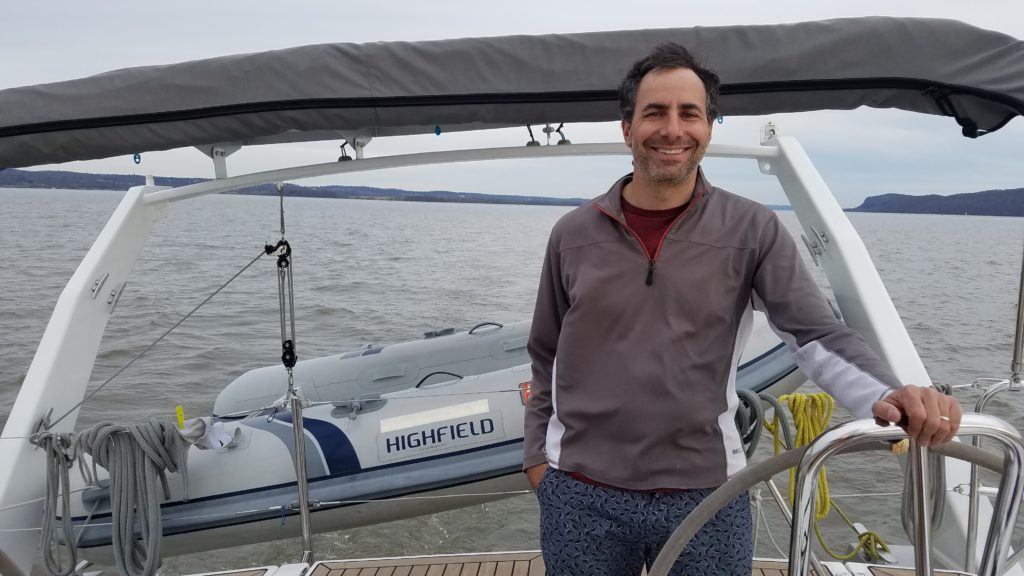
Wow! I can’t believe the growth on the bow thruster! Gross! LOL
I was curious about a few things…
1) How were you able to antifoul the swing keel when the boat was that near the ground (as in your pic)?
2) Wouldn’t mounting the water maker in the other cabin (technical space) be better for noise control / not getting in the way of guests? Is there not enough space there?
3) Does the bow thruster have a sacrificial anode?
4) Are the boat’s rudders aluminum or fiber glass?
Love the technical posts! Keep these up!
Thank you for the positive feedback. I will do more technical posts with this encouragement. To answer your questions:
1) There was enough room to crawl under the keel and reach up into the centerboard trunk with a small roller on a 24″ handle. It was not fun but was mostly effective. Next haul out we will have them block the boat up higher.
2) There would be logic to mounting the watermaker in the technical room in terms of noise. There is room there. However, there are several advantages to where I mounted it. For one, it is the location that Allures planned for a watermaker. We ordered a “pre-installation” watermaker package with the boat. This included thru hulls for raw water and brine discharge and a welded mounting base for the pumps, all of which was in the starboard aft cabin. I suspect we could have asked Allures to install this on the port side. Regardless, in the starboard aft cabin, under the bed, there is a long compartment to elegantly accommodate two full length RO membranes. Additionally, the main electrical bus bars are adjacent to where we installed the watermaker, making electrical runs short and reducing wire size. The water tank and test outlet are installed on the port side of the boat, so those plumbing runs are longer, but plumbing lines are less sensitive to length than electrical in this case (and also much less expensive). I don’t think we will be making water when people will want to sleep in the rarely occupied aft cabin, so I am not worried about the noise.
3) The Max-Power bow thruster leg is all composite construction. The entire leg is fully isolated electrically from the hull and thruster motor / electronics. The propellers are heavy duty plastic. No anode is required. This is all particularly good for an aluminum hulled boat.
4) The boats rudders have aluminum structural frames and post. The shell is fiberglass. The assembly is made by Jefa Steering Systems – ALLUR-CO46RUD.
Ah! That makes sense. Especially the long membrane, and the wire run given the 12v system. Thanks for quick response and details! I got my eye on possibly getting a 45.9 myself. Your website has been very helpful.
Another question I thought of afterwards: You installed pad-eyes for the drogue, but I noticed in your pics you already have two cleats just inside the aft arch. Was that done just to prevent chafe, or is that part of the boat not supported enough, or some other reason? What are you using to attach the drogue to the pad-eyes?
Our inboard aft cleats are welded on and are pretty massive. They are likely plenty strong to handle the drogue loads, but this is difficult for me to verify. The advantages of the pad-eyes include that they are further outboard, result in a perfectly fair lead, and have a quantified strength that I am confident exceeds Don Jordan’s calculated loads. I do know another Allures 45.9 owner who is confidently planning to utilize the inboard cleats for their drogue. So, perhaps the pad-eyes are not required.
We have massive dyneema soft shackles with chafe guards to attach the bridle legs to the pad-eyes. With a breaking strength of 42,000lbs each, these are overkill. But, they are light, easy to source, and less expensive than adequate metal shackles.
Nice. Thanks! Have a great season!